Bu makale, güneş enerjisi sektöründe fotovoltaik (FV) modül üretim süreçlerini, performans testlerini, sektördeki Tier-1 FV modül üreticilerinin kalite kriterlerini ve üretim denetimlerini detaylı olarak ele almaktadır. FV modül üretimi, yüksek kalite standartlarının ve performansın sağlanması için titiz bir süreç gerektirir. Üretim aşamaları, hammaddenin seçimi ve hazırlanmasından başlayarak hücre üretimi, modül oluşturma ve modül montajına kadar uzanır. Her aşamada kalite kontrol ve performans testleri düzenli olarak uygulanır. Performans testleri, FV modüllerinin dayanıklılığını, verimliliğini ve uzun vadeli performansını değerlendirmek için kritik öneme sahiptir. FV modüllerinin güneş ışığını verimli şekilde elektriğe dönüştürme yeteneği, dayanıklılığı ve uzun ömürlülüğü kalite kriterlerinin temelini oluşturur. Bu üreticiler, genellikle sektördeki iyi uygulamalara ve yüksek kalite standartlarına uyarlar. Üretim denetimleri, kaliteyi ve uyumluluğu sağlamak için hayati öneme sahiptir. Bu denetimler, hammaddenin seçiminden başlayarak montaj aşamasına kadar her adımda kaliteyi izler ve uyumluluğu sağlar. Güneş enerjisi endüstrisindeki sürekli gelişmeler, FV modül üretim süreçlerinin ve kalite standartlarının sürekli olarak iyileştirilmesini gerektirir. Bu unsurların bir araya gelmesi, güvenilir, etkili ve sürdürülebilir FV modül sistemlerinin geliştirilmesine önemli katkılar sağlar.
Fotovoltaik Hücre Nedir?
Güneş enerjisini elektrik akımına dönüştüren teknolojiye fotovoltaik (FV) denir. Güneş enerjisini kullanılabilir güce çeviren fotovoltaik teknolojisi ışıktan elektrik üretimi gerçekleştirir. Güneş ışığını doğrudan elektrik enerjisine dönüştüren yarıiletken maddelere fotovoltaik hücre denir. Fotovoltaik hücre üzerine düşen fotonlar elektrik enerjisine evrilir. Güneş ışınımları yarıiletken madde üzerine düştüğü zaman ışınımın enerjisi, madde atomlarının en dış yörüngesinde bulunan atomlarını hareket ettirir. Bu olaya fotoelektrik olay denir. Gevşek atomların hareketi ile iletkenler üzerinde elektrik akımı oluşur. Elektronlar ise taşıdıkları enerji miktarlarını karşılaştıkları engeller üzerinde bırakarak iş yapar. Yarıiletken teknoloji ile üretilen fotovoltaik hücreler silikon temellidir. Fotovoltaik hücreler birbirine seri ve paralel bağlanarak bir yüzeye monte edilir. Güç çıkışını arttırmak için hazırlanan bu sisteme fotovoltaik modül denir. Şekil 1’ de fotovoltaik hücre, Şekil 2’ de fotovoltaik modül ve fotovoltaik panel görünümü verilmiştir[1].
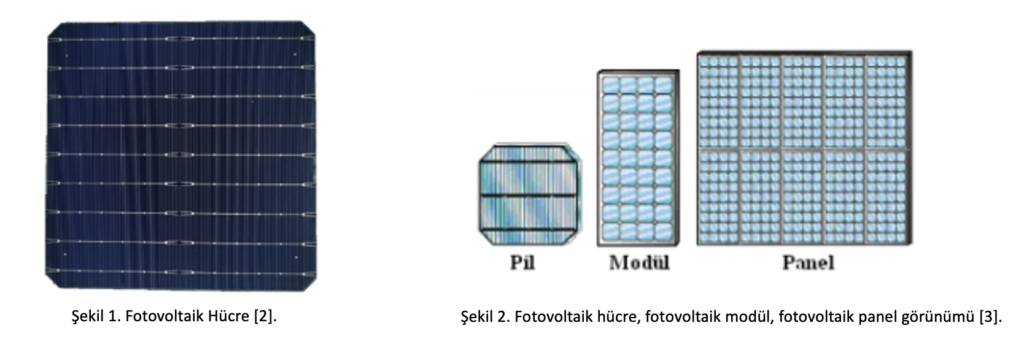
Monokristal ve Polikristal Hücre
Bu tür fotovoltaik hücrelerde hammadde olarak yüksek saflıkta silisyum kristalleri kullanılır. Monokristal ve polikristal fotovoltaik hücreler olarak iki ana çeşidi bulunur.
Verimleri diğer yöntemlerle üretilen hücrelere göre daha yüksek ve ömürleri daha uzundur.
Kristal yapıları düzenli olan monokristal fotovoltaik hücrelerin kristal yapıları düzenlidir ve bu yüzden üretimiz zor, maliyeti yüksektir.
Polikristal fotovoltaik hücrelerde ise kristal yapısındaki çok az miktarda olan bozukluklar bu tip hücrelerin verimlerinin bir miktar düşmesine sebep olur. Ancak monokristal fotovoltaik hücrelere kıyasla üretimindeki kolaylık ve maliyetinin düşük olması tasarımlarda bu tip hücrelere yönelimin artmasına neden olmaktadır[4]..
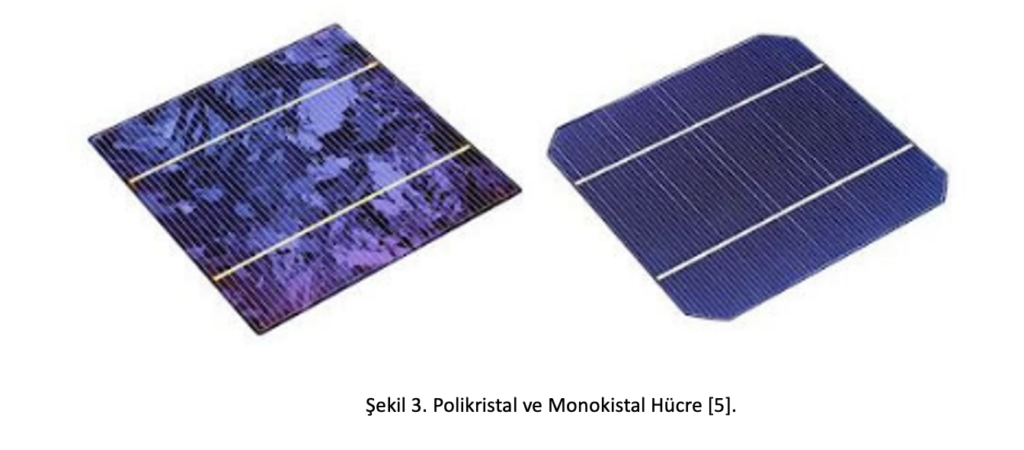
Fotovoltaik Modül Nasıl Oluşur?
Fotovoltaik modüller, monokristal veya polikristal hücrelerin seri veya paralel bağlanmasıyla oluşturulur ve istenilen akım, gerilim ve güç değerlerine ulaşmak amaçlanır. Bu hücreler robotlar yardımıyla lehimlenir. Lehimlemenin ardından hücreler, koruyucu ve soğurma özelliği yüksek etilen-vinil-asetat (EVA) adı verilen bir malzemenin üzerine yerleştirilir. EVA, temperlenmiş cam üzerine serilir ve hücreleri dış etkenlerden korur. Fotovoltaik hücrelerin hem ön hem de arka yüzeylerinde EVA bulunur. Arka kısımda ise TEDLAR adı verilen, güneş panelini UV ışınları, yüksek sıcaklık ve nem gibi etkenlere karşı koruyan bir malzeme kullanılır. EVA ve TEDLAR ile korunan hücreler, özel laminatörlerde yüksek sıcaklık ve basınç altında işlenerek tek bir bütün haline getirilir. Ardından, gölgelenme etkilerini en aza indiren By-Pass diyotları içeren bağlantı kutusu modüle yerleştirilir. Tüm bu işlemler sonucunda fotovoltaik modül, bir güç üreteci haline gelir[1].
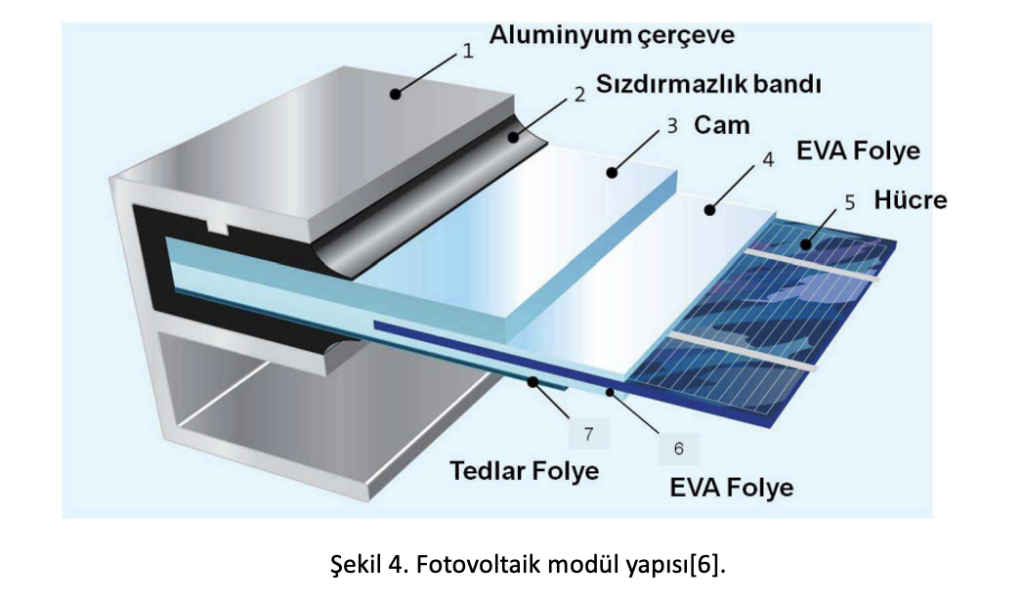
Fotovoltaik Modül Üretim Aşamaları
TS EN IEC 61215 Karasal Fotovoltaik (FV) modüller – Tasarım yeterliliği ve tip onayı
IEC 61215 standardı, genel açık hava iklimlerinde uzun süreli çalışmaya uygun karasal fotovoltaik (FV) modüllerin tasarım yeterliliği ve tip onayı için IEC gerekliliklerini ortaya koyar. Bu standart, kristal silikon modül türleri ve ince film modüller gibi tüm karasal düz plaka modül malzemelerine uygulanmak üzere tasarlanmıştır[7].
TS EN 61730 Fotovoltaik (FV) modül güvenlik niteliği
IEC 61730 bir FV modülünün güvenlik yeterliliği için yerine getirmesi gereken testleri listeler. IEC 61730-2 ve IEC 61730-1 birlikte güvenlik yeterliliği için uygulanır[8].
Bu standartta belirtilen test sıralaması, FV modüllerinin tüm olası uygulamalarında karşılaşılabilecek tüm güvenlik unsurlarını test etmeyebilir. Yüksek voltajlı bir sistemde kırık bir FV modülünün oluşturabileceği elektrik çarpması tehlikesi gibi bazı konular, sistem tasarımı, konumu, erişim kısıtlamaları ve bakım prosedürleri ile ele alınmalıdır[8].
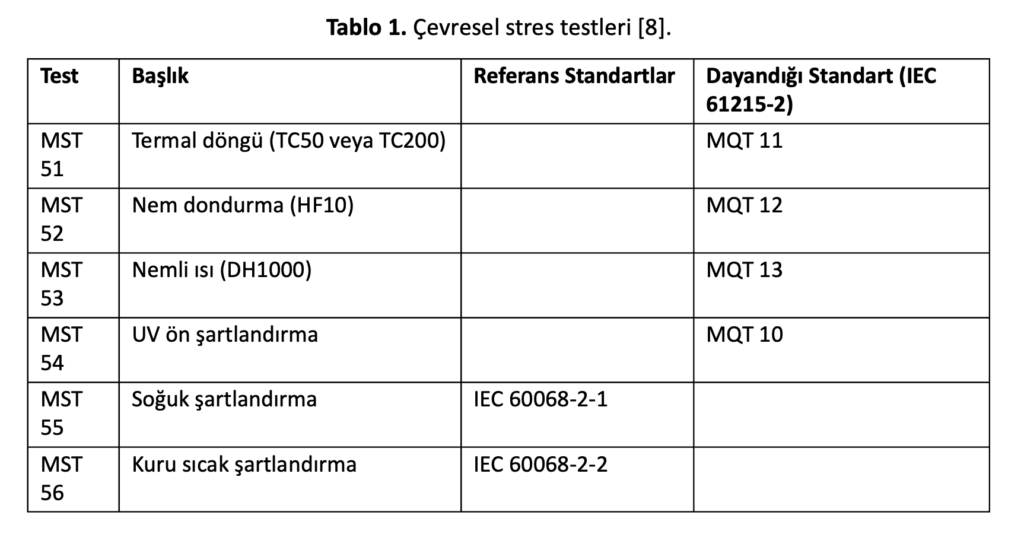
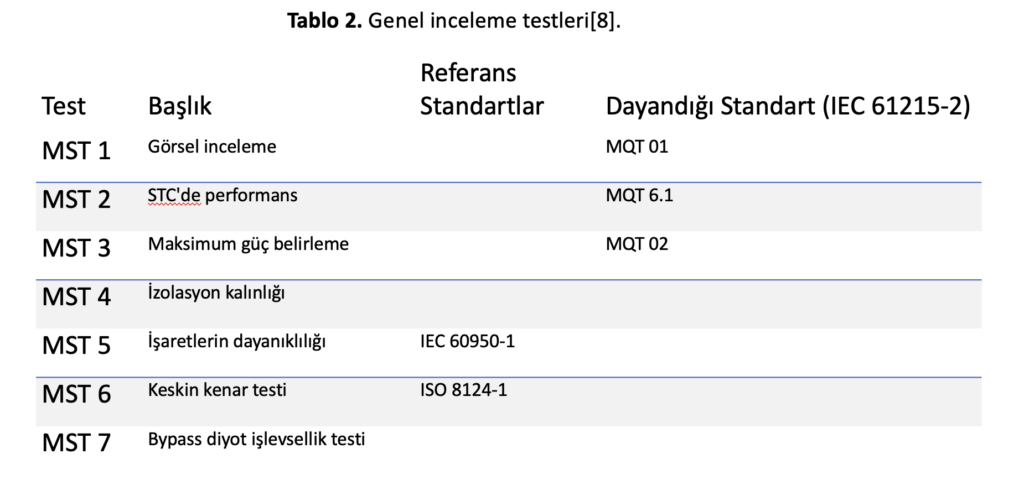
FV panel fabrikaları, panel üretiminde kullanacağı tüm hammaddeleri, alternatif markalarıyla birlikte birkaç kombinasyonunu gerçekleştirir. Bütün malzemeler ve özel bileşenlerini içererek hazırlanan bu kombinasyonlar Constructional Data Form (CDF)’ da yer alır. CDF’ e göre paneller üretilir ve bu panellere IEC 61215/IEC61730 standartlarının gereği termal çevrim testi, nem donması testi, nemli ısı testi, mekanik yükleme testi gibi birçok test uygulanır. Güneş panelleri; IEC 61215 ve IEC 61730 standartlarına göre girdiği testleri başarı ile geçerse sertifika almaya hak kazanır. Bu aşamadan sonra panellerin onaylı bir CDF’ i ve CDF’ e ek IEC 61215/IEC 61730 sertifikaları olur. Fabrika, panelleri BOM List adı verilen malzeme listesine göre üretir ve bu BOM List CDF’ te yer alan malzemeleri içermelidir.
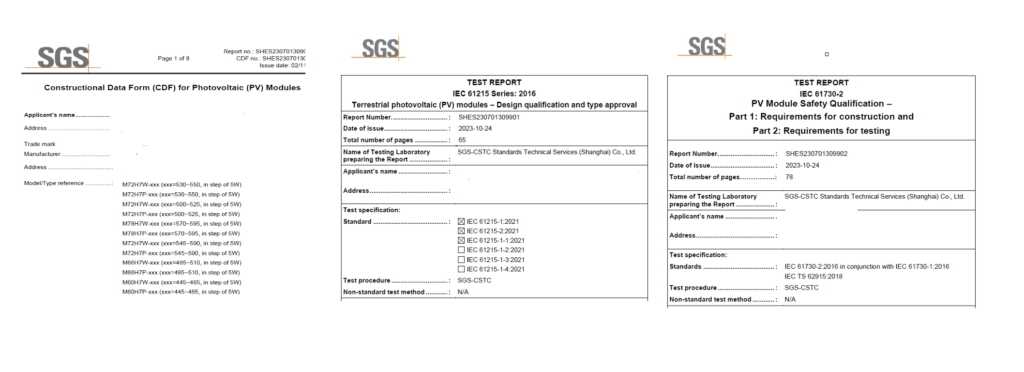
Hücre Testi
Güneş hücresi testi, güneş paneli üretiminin ilk işlemi olarak uygulanır. Test yapılırken hücrenin bir solar simülasyon altında elektrik performansı test edilir. Ayrıca kalite testi olarak da yüzey kalitesi, kırılmalar ve çatlaklar gibi istenmeyen olumsuz etkiler kontrol edilir[9]. Şekil 5’ te hücre kesme makinası gösterilmiştir.
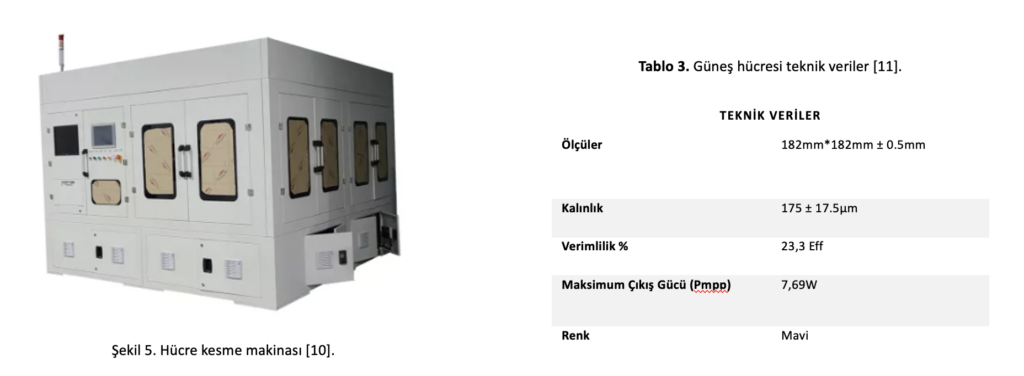
Cam Yükleme
Güneş paneli üretiminde kullanılan camlar, düşük demir oksit içeriğine sahip düz veya buzlu temperli camlardır. Düşük demir oksit oranı, camın ışık geçirgenliğini artırır. Üretim hattında, camlar otomatik robot kolları tarafından hassas bir şekilde yüklenir. Robot kollarının yüksek hassasiyetle çalışması, camların yükleme sırasında kırılma ve çatlama riskini en aza indirir. Camlar yüklendikten sonra yüzey kontrolü ve temizleme işlemlerinden geçer. Bu aşamada, yüzeydeki çatlaklar ve deformasyonlar tespit edilir[9]. Şekil 6 ‘ da FV modül camı, Şekil 7’ de FV modül üretimi yapan bir fabrikanın cam yükleme makinası görülmektedir.
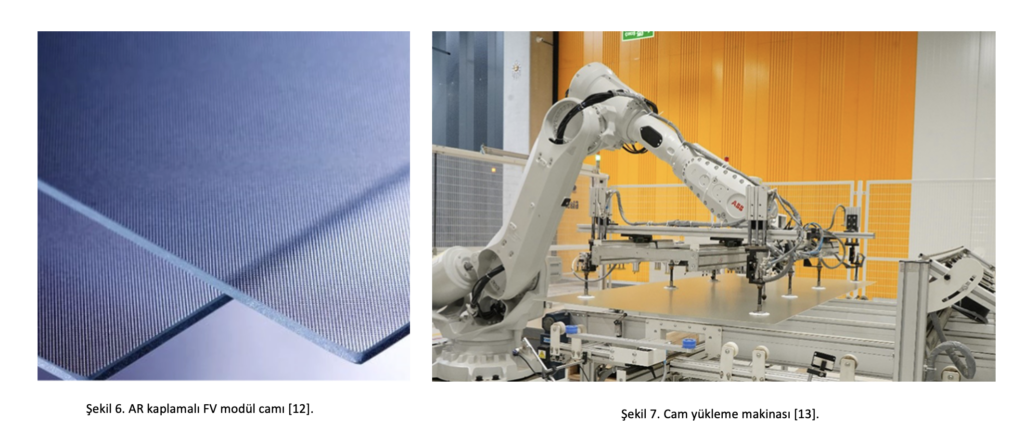
Folyo Serme Hattı
Güneş paneli üretim sistemlerinde elektrik üretimini daha verimli hale getirmek ve hücreleri darbelere karşı korumak amacıyla EVA (etilen vinil asetat) solar filmi kullanılır. EVA folyolar, bu üretim hattında cam ile hücreler arasında yer alacak şekilde birleştirilir[9]. Şekil 8’ de EVA serme makinası görülmektedir.
EVA, özel bir tabakadır ve cam ile hücreler arasında, ayrıca hücreler ile arka kaplama (backsheet) arasında yer alır. Her iki tarafına uygulanan EVA, sıcak laminasyon yöntemiyle eritilerek güneş hücrelerini tamamen sarar. Bu işlem, panelin dayanıklılığını artırırken, su ve mikro toz gibi unsurların içeri sızmasını engeller. Aynı zamanda darbe ve titreşimleri emerek güneş hücrelerini korur[14].
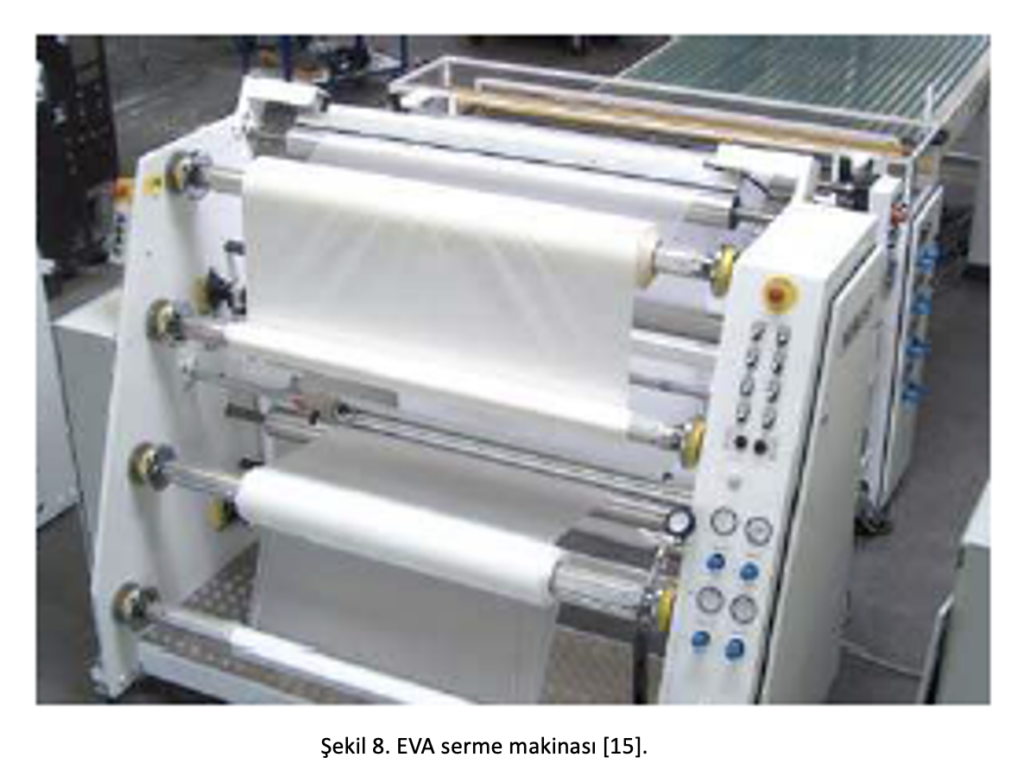
Stringer ve Lehimleme Hattı
Güneş hücreleri üzerindeki mikro çatlaklar ve deformasyonlar tespit edildikten sonra, üretim hattında hücreler dikkatlice hizalanarak dizilir. Stringer makineleri, hücrelerin üzerine lehim pastası püskürttükten sonra kızılötesi veya lazer kullanarak lehimleme işlemini gerçekleştirir[9]. Şekil 9’ da stringer makinası görülmektedir. Stringer makinasında hücrelerin üzerine ribbon adı verilen iletken teller lehimlenir. Şekil 10’ da lehimleme işlemine ait görsel verilmiştir.
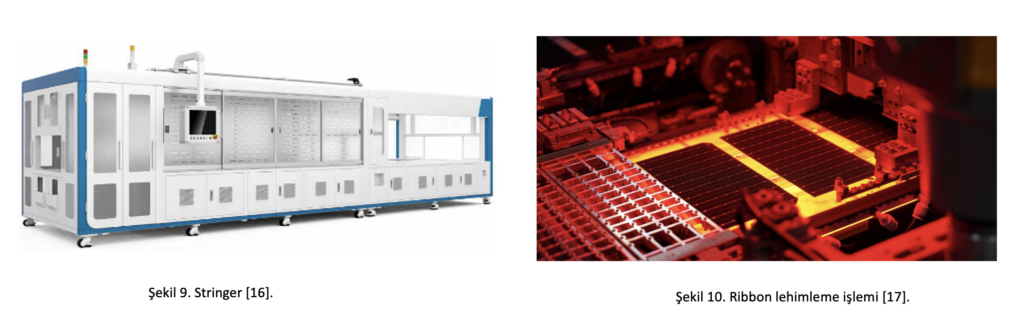
Laminasyon Hattı
FV modül stringer bölgesinden çıktıktan sonra arka tarafına tekrar EVA malzemesi ve üzerine ya yine AR kaplamalı cam ya da backsheet adı verilen arka tabaka serilerek laminasyon hattına gönderilir. Burada yüksek sıcaklık ve basınçta tüm malzemeler iç içe geçer ve bir bütün halini alır.
Arka tabakalar, güneş panellerinin dış katmanıdır ve iç devrelerin dış ortamla elektriksel izolasyonunu sağlar. Bu katman, panelin zorlu çevre koşullarından korunmasında kritik bir rol oynar. Güneş panellerinin panel ömrü boyunca dayanıklılığını artırır ve güvenlik riskini azaltır[14]. Şekil 11’ de FV modül için kullanılan backsheet yer almaktadır. Laminasyon hattında, EVA materyalinin sabit bir zamanda ve ısıda tamamen eriyerek, şeffaf bir görüntü alması ve hücreler ile tüm paneli çok iyi kavraması gerekmektedir[9]. Şekil 12’ de laminasyon hattı yer almaktadır.
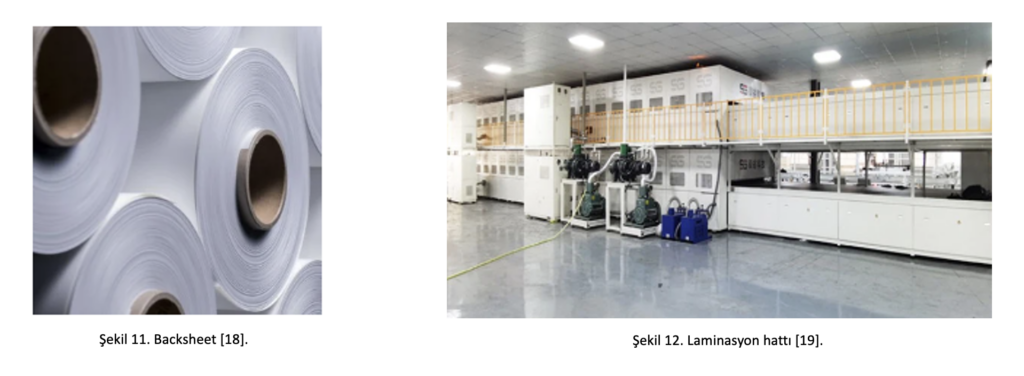
Pres Hattı
Panel ve çerçevelerin kenar düzeltmeleri ve kesimleri yapıldıktan sonra çerçevenin oturtulması için bu hatta gönderilir. Çerçeve işlemi tamamlandıktan sonra, panellere bağlantı kutusu monte edilir[9]. Şekil 13’ te çerçeve press hattı yer almaktadır. FV modül üretiminde kullanılan alüminyum çerçeveler, montaj deliklerinin uygun tasarımı, set ağırlıkları, kaplama kalınlığı ve içeriğindeki elementlerin oranları gibi faktörlere dikkat edilmesi gereken önemli bileşenlerdir. Alüminyum çerçevelerde düşük demir oranı, paslanma riskini azaltır ve eloksal kaplama kararmayı önler[14]. Şekil 14’ da çerçeve gösterilmiştir.
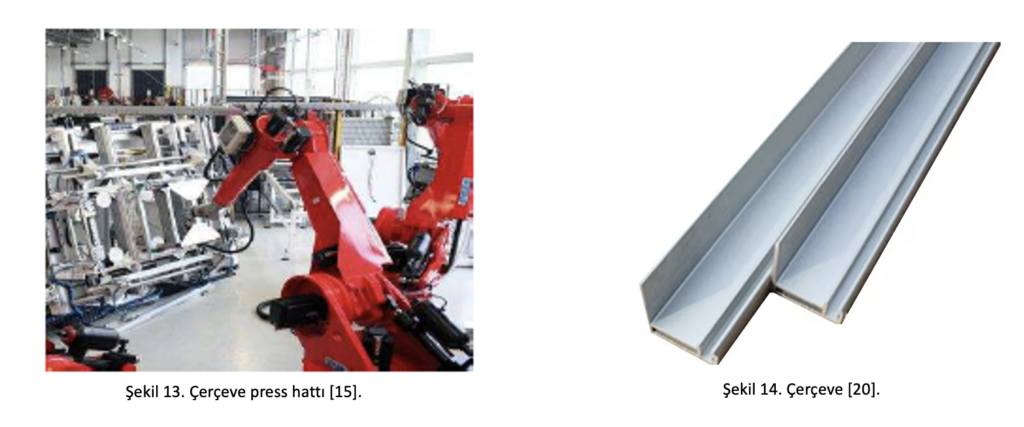
Junction Box Bağlama
Çerçeveden çıkan modüllere bağlantı kutusu (junction box) takılır. Fotovoltaik güneş panellerindeki hücreleri birbirine seri olarak bağlayan junction box, üretilen elektriği dış hatlara ileterek paneli elektriksel olarak korur. İçerisindeki diyotlar, güneşten gelen UV ışınlarına karşı koruma sağlar. Aynı zamanda bu kutu, panelde oluşabilecek arızaların tespit ve tamiri için erişim sağlar[14]. Şekil 15’ de bağlantı kutusu yer almaktadır.
Üretim denetimi boyunca gerçekleştirilen hammadde kontrolleri aynı şekilde backsheet, bağlantı kutusu ve çerçeve için de yapılmalıdır. Burada dikkat edilmesi gereken husus bu ürünlerin marka modellerinin CDF’ te yer almasıdır. Özellikle bağlantı kutusu için bu konuyu ele alacak olursak kontrol edilmesi gereken üç husus vardır. Bunlar, bypass diyor, kablo ve konnektördür. Bu üç elaman bağlantı kutusunu oluşturur. Her bağlantı kutusu markası bu üç eleman için farklı özellikte ürün kullanabilir. Örneğin anma akımı 25A olan bir bağlantı kutusunda 4045 olarak kodlanan bypass diyot kullanılırken 30A için 5045 kullanılabilir. Bu kombinasyonların da CDF’ e uygun olması gerekmektedir.
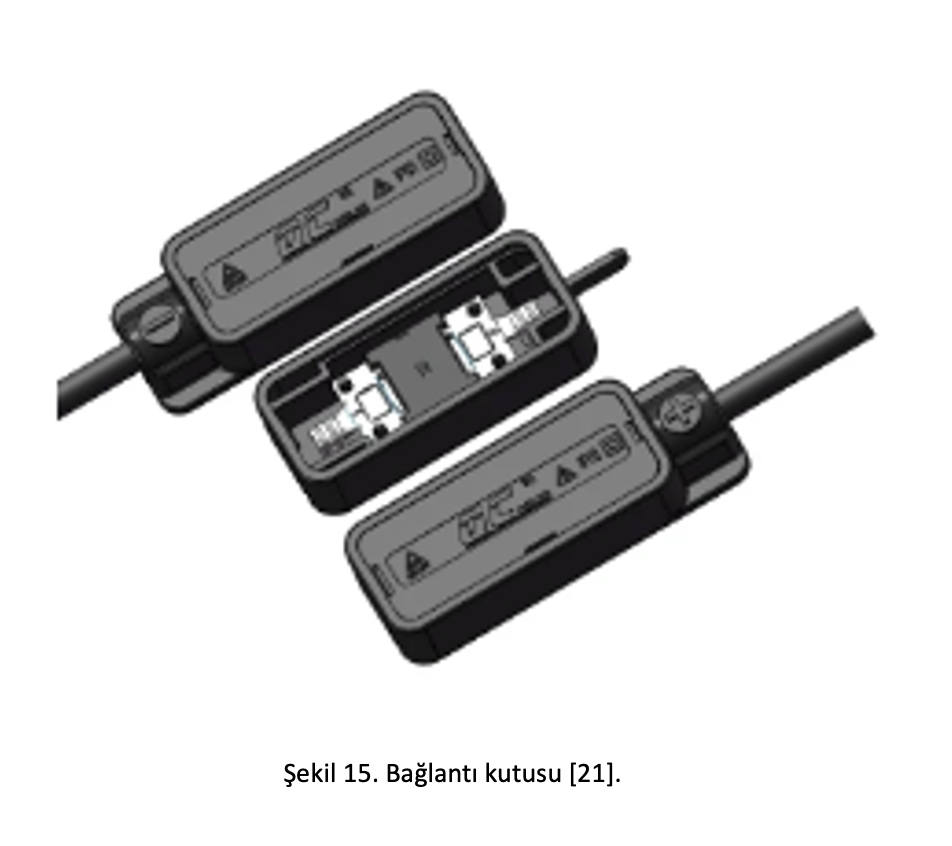
IEC 61215/ IEC 61730 Kapsamında Uygulanan Testler
Gözle Muayene (Visual Inspection)
FV modüller 1000 lüksten az olmayan bir aydınlanma altında aşağıdaki koşullar için muayene edilir.
·Çatlak, eğik, yanlış hizalanmış ya da yırtık dış yüzeyler
·Kırık, çatlak hücreler,
·Hatalı bağlantı noktaları veya birleşmeler,
·Birbirine veya çerçeveye temas eden hücreler,
·Yapıştırıcı bağların bozukluğu,
·Bir hücre ve modül kenarı arasında kabarcık ya da katlarına ayrılma sonucu oluşan sürekli bir yol,
·Plastik malzemelerin yapışık yüzeyleri,
·Akım geçen elektrikli parçalara maruz kalan hatalı sonlandırmalar,
·Performansı etkileyebilecek diğer tüm koşullar [22].
Gözle görülemeyen mikro kırıkların tespiti amacıyla FV modüllerin Elektroluminesans (EL) görüntülerine bakılır.
Elektrolüminesans görüntüleri genellikle loş ortamlarda elde edilir ve genellikle gri tonlamalıdır. Bu tür görüntülerdeki kusurlar genellikle karanlık bölgelerde belirir; özellikle kırıklar ve diğer hatalar, siyah çizgiler veya koyu lekeler olarak ortaya çıkar. Elektrolüminesans görüntüleme, birçok üretici firmada yaygın olarak kullanılan bir kusur tespit yöntemidir[23]. Şekil 16’ da FV modüle ait EL görüntüsü yer almaktadır.
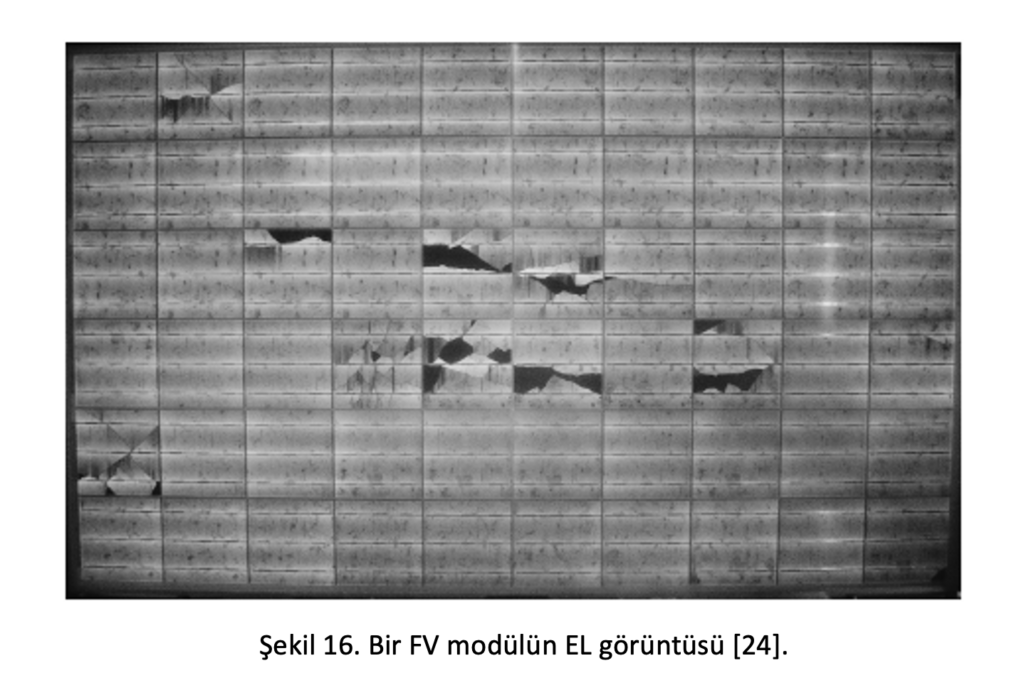
Maksimum Güç Tayini (Maximum Power Determination)
1000W/m² ışımada ve 25°C sıcaklıkta FV modülün güç tayini yapılır[22].
Yalıtım Deneyi (Insulation Test)
Bu test ile modülün akım taşıyan bölümleri ile çerçeve veya çevre arasında iyi yalıtım sağlanıp sağlanmadığı belirlenir. 0,1 m2 ’den daha az alana sahip modüllerin yalıtım direnci 400 MΩ’dan az olmamalıdır. 0.1 m2 ’den daha fazla alana sahip modüller için 500 V veya azami sistem voltajının hangisi büyükse o voltajda ölçülen yalıtım direncinin modül alanıyla çarpımının değeri 400 MΩ x m2 ’den az olmamalıdır[22]. Şekil 17’ de TSE yalıtım deneyi kabini yer almaktadır.
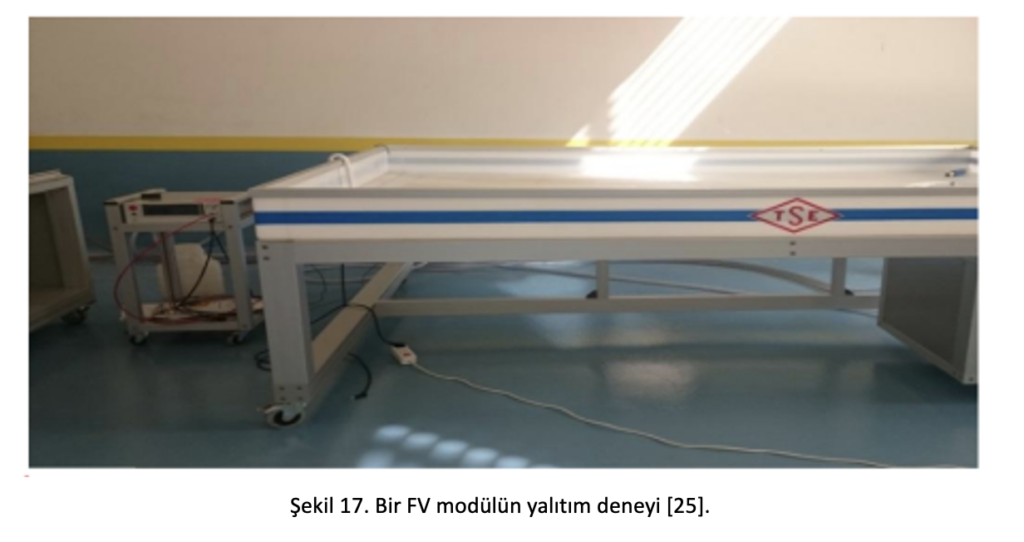
Sıcaklık Katsayılarının Ölçümü (Measurement of Temperature Coefficients)
Kristal teknolojisine sahip monokristal ve polikristal hücrelerin sıcaklık arttıkça güçleri düşer. Düşük sıcaklık katsayısı, sıcaklığın yükseldiği durumlarda enerji kaybını azaltır. Modül istenilen sıcaklığa ulaştığında, ISC, VOC ve tepe gücü ölçülür. Modül sıcaklığı, en az 30°C’lik ilgilenilen aralık üzerinde yaklaşık 5°C’lik adımlarla değiştirilir ve ISC, VOC ve tepe gücü ölçümleri tekrarlanır[22]. Şekil 18’ de ilgili deney gösterilmektedir.
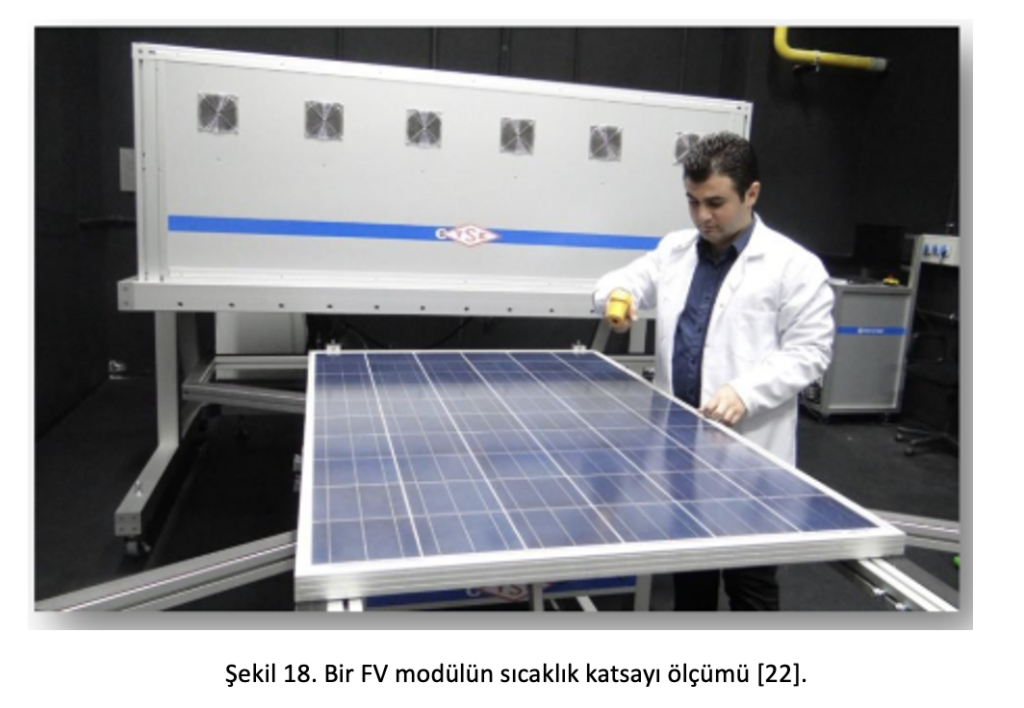
Sıcak Leke Dayanımı Deneyi (Hot-Spot Endurance Test)
Bu deneyin amacı, modülün sıcak nokta ısınma etkilerine dayanma yeteneğini belirlemektir, örneğin lehimin erimesi veya muhafazanın bozulması ısınma etkisi yaratabilir. Bu kusur, çatlak veya uyumsuz hücreler, ara bağlantılı kusurlar, kısmi gölgelenme veya lekeler tarafından da arttırılabilir. Gözle görülür kusurlar olmamalıdır, azami çıkış gücündeki azalma deneyden önce ölçülen değerin %5’ini geçmemelidir ve yalıtım direnci başlangıç ölçümlerini karşılamalıdır[22].
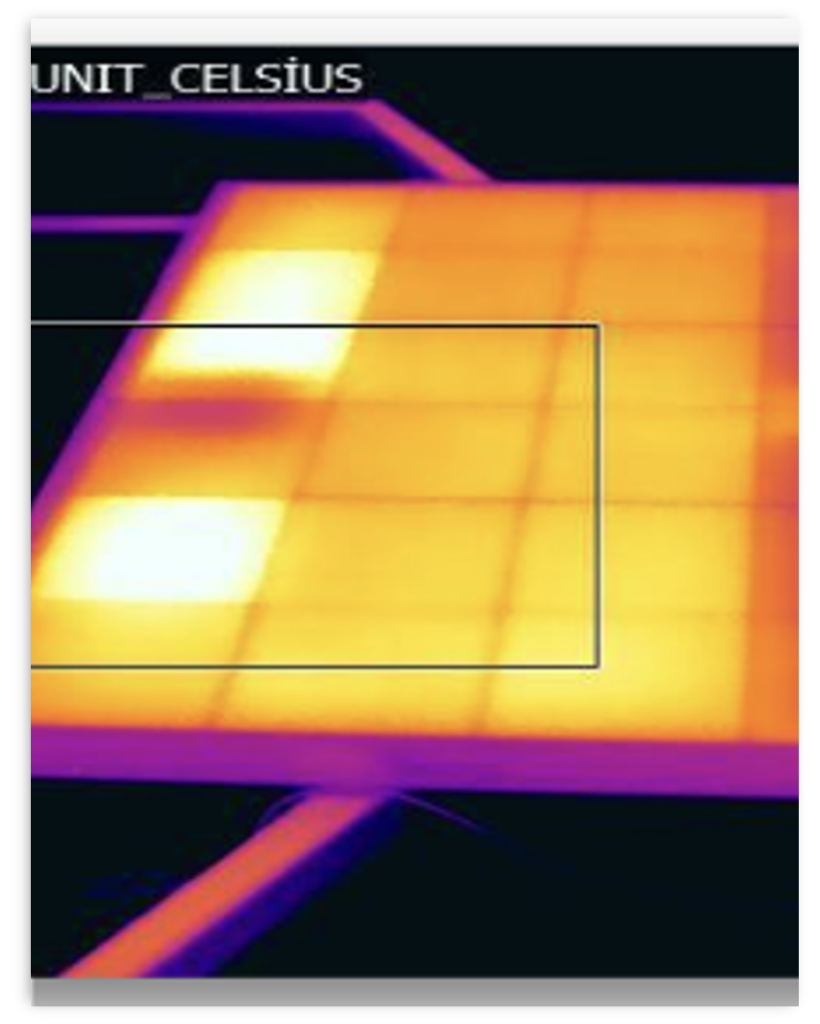
Ultraviole Şartlandırma Deneyi (UV Preconditioning Test)
FV modül ısıl çevrim/nem donma deneylerinden önce UV kötüleşmesine duyarlı olan malzemelerin ve yapışkan bağlayıcıların tanımlanması için mor ötesi (UV) radyasyonla ön koşullandırmaya tabii tutulur. Modülün sıcaklığı, UV ışığı ile ışınlandığı sırada 60ºC ± 5 ºC’de, 280 nm ve 385 nm arasında dalga boyu aralığında, toplam 15 kWh/m2 ‘lik, dalga boyu bandı ile UV ışımasına maruz bırakılır. [22].
Isıl Çevrim Deneyi (Thermal Cycling Test)
FV modülün termal uyumsuzluğa, yorgunluğa ve sıcaklığın tekrarlanan değişiminden kaynaklanan diğer gerilmelere karşı dayanma yeteneği belirlenir. -40 °C ile +85 °C aralığında 50 ve 200 çevrim uygulanır. Deney sırasında, akım akışında kesinti olmamalıdır[22].
Nem-Donma Deneyi (Humidity-Freeze Test)
FV modülün sıfırın altı sıcaklıkları takiben yüksek sıcaklık ve nem etkilerine dayanma yeteneğini belirlenir. Bu bir ısıl şok deneyi değildir. +85 °C’ ve -40 °C de, % 85 RH bağıl nemden 10 çevrim uygulanır[22].
Yaş Sıcaklık Deneyi (Damp-Heat Test)
FV modülün, neme, uzun dönem nüfuz etkilerine dayanma yeteneğini belirlenir. 1000 saat, +85 °C , % 85 RH bağıl nemde test uygulanır[22].
Yaş Kaçak Akım Deneyi (Wet Leakage Current Test)
Bu deney, ıslak çalıştırma şartları altında FV modülün yalıtımını değerlendirir ve yağmur, sis, çiy veya erimiş kardan kaynaklı rutubetin modül devresinde korozyona, topraklama arızasına veya güvenlik riskine sebep olacak modül devresinin aktif kısımlarına girmediğini doğrular[22].
•Direnç: 3.500Ω veya daha az
•Yüzey Gerilimi: 0.03 N/m veya daha az
•Sıcaklık: 22 ºC ± 3 ºC
-0.1 m² den daha az alana sahip modüller için yalıtım direnci 400MΩ dan az olmamalıdır. 0.1 m² den daha geniş alana sahip modüller için ölçülen yalıtım direncinin modülün alanı ile çarpımı, 40 MΩ.m² den az olmamalıdır[22].
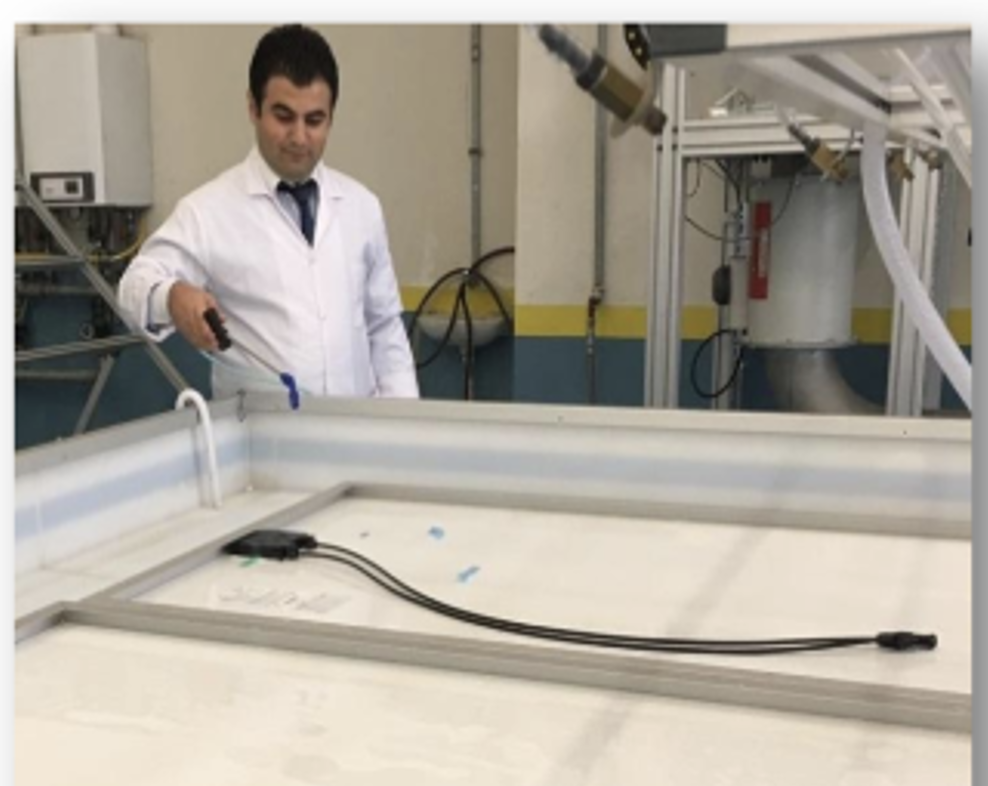
Mekanik Yük Deneyi (Mechanical Load Test)
Bu deneyin amacı, fotovoltaik (FV) modülün rüzgara, karaya, statik yüklere veya buz yüklerine karşı dayanıklılığını belirlemektir. Deney sırasında modülün iç devresinin elektriksel bütünlüğünü sürekli olarak izleyebilmek için modül beslenir. Ön ve arka yüzeyine 2400 Pa’lık bir yük, üç çevrim boyunca 1 saat süreyle uygulanır[22].
2400 Pa, güvenlik faktörü 3 olan ve 130 km/sa (yaklaşık ± 800 Pa) hızındaki şiddetli rüzgarlar için bir referans olarak kabul edilir. Eğer modül ağır kar veya buz birikintilerine dayanıklı olması gerekiyorsa, modülün ön yüzeyine uygulanacak kuvvet, son çevrim için 2400 Pa’dan 5400 Pa’ya yükseltilir. Deney sırasında kesintisiz bir açık devre hatası tespit edilmemelidir ve gözle görülebilir büyük kusurlar olmamalıdır. Ayrıca, maksimum çıkış gücündeki azalım, deney öncesinde ölçülen değerin %5’ini aşmamalıdır[22].
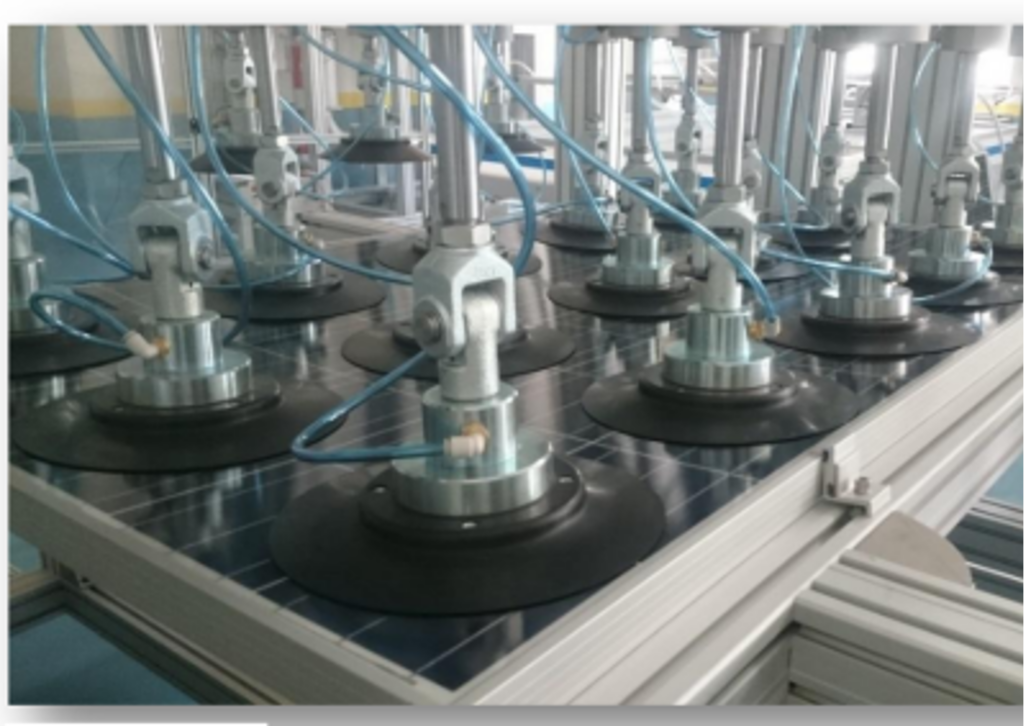
Elektroluminesans (EL) Görüntüleme
Fotovoltaik panellerin kusurlarının erken tespiti, sistemlerin verimliliğini, güvenilirliğini ve uzun ömürlülüğünü sağlamak için kritik öneme sahiptir. Kusurlar, panel verimini düşürüp enerji üretimini sınırlayabilir ve güvenlik riskleri oluşturabilir. Bu tespitler, görsel inceleme, elektriksel testler ve performans izleme gibi yöntemlerle yapılır ve uzman ekipler tarafından gerçekleştirilir. Özellikle elektrolüminesans (EL) görüntüleme, panellerdeki kırıklar ve diğer kusurları belirginleştiren bir yöntem olarak yaygın kullanılır. EL cihazları, panellere uygulanan DC güçle oluşan ışımaları özel kameralarla yakalayıp kusurları tespit eder. Bu süreç, panellerin üretim ve işletim aşamalarında performans ve ömrünü artırmak için gereklidir ve yerel mevzuatlara uygun olmalıdır. Kusurların tespiti ve giderilmesi, sistemin optimum performansını sağlayarak işletme maliyetlerini düşürür ve çevresel faydaları artırır[23].

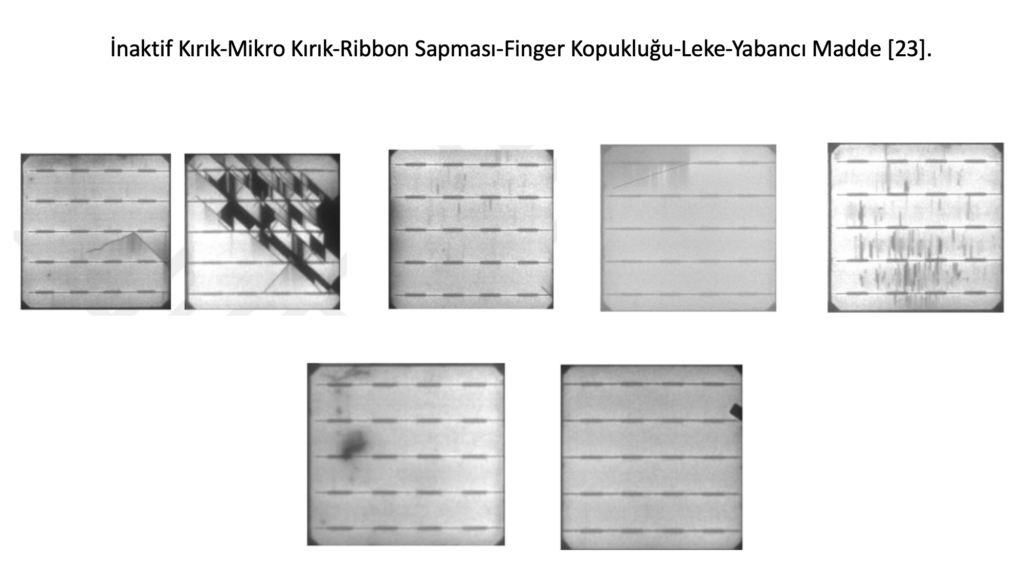
Yazar:
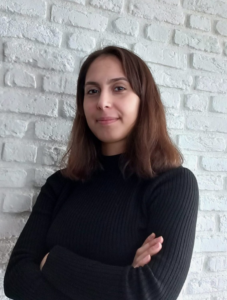
Melisa Ekşi